MDF wood process application
Sealers
Sealer coats is the first finishing step. It is used to fill-up gaps and irregularities on the wood surface but also ensures a non penetration of the addtional layers. Generally on MDF, only one layer of sealer is needed.
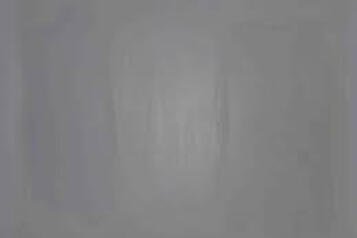
The issue is that uneven applications of sealers will allow the primer layer to penetrate the wood and generate default aspects after sanding.
To solve any uneven applications, we recommend Airmix®:
- For manual application, use the AIRMIX® XCITE® LIGHT MANUAL SPRAY GUN gun with our genuine Airmix® tip
- For automatic application, use the AVX AUTOMATIC AIRMIX® SPRAY GUN with our genuine Airmix® tip
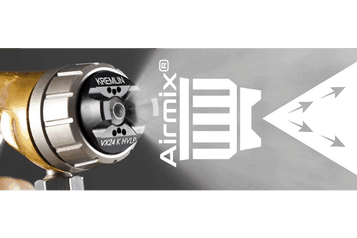
When you need an event layer on solid wood & glossy finishing on MDF, Airmix® technology is particularly recommended for applying clear coat and top coat.
Clear coat and top coat need to have certain thinness. In Airspray, you will need too many layers to achieve the film thickness you need and you will loose lot of paint with the overspray. In Airless® , you will apply too much paint.
Thanks to the low speed of the paint particle and adding 0.5 bar of air atomization, Airmix® keeps a maximum of solvent on the color particle during spraying. The 0.5 bar additional air accompanies the paint particle to the substrate and prevents air movement around the particle so as to avoid "desolvation." When you spray clear coat or top coat, the solvent aids in smoothing the paint for a glossy and even finish. The avoidance of "desolvation" along with our Airmix® technology helps in detering orange peel effects
Primers (UV and non-UV products)
The primer is used to block the fibers of the wood to obtain the smoothest surface possible after sanding
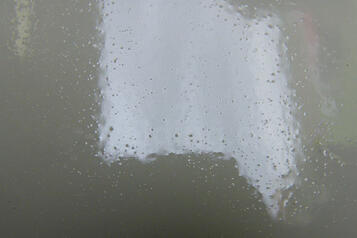
This issue is a consequence of some air which remains enclosed in the film build.
To solve any bubbling effect, we recommend using Airless® with Skill technology: .
- For manual application, use the SFLOW™ 275 & 450 AIRLESS® MANUAL SPRAY GUN gun with a Skill tip
- For automatic application, use the ASI AIRLESS® AUTOMATIC SPRAY GUN with a Skill tip
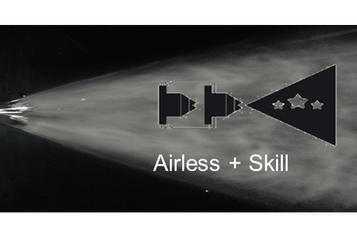
Airless® - combined with Skill tip technology - is recommended to apply UV paint and primer on solid wood & MDF wood.
When you spray UV paint, the addition of air atomization will create bubbling in the film build during the application. Compared to a classical Airless® application, the Skill tip technology uses half of the pressure to apply the paint particles and by this fact the desolvation is limited. This way you can avoid bubbling and get a nice finishing effect.
When you spray Primer, you need a certain layer before sanding. The low paint speed of the Skill tip technology -compared to a classical Airless® - leads to less overspray and allows to spray closer to the substrate, which in turn allows for better transfer efficiency and a thicker film build.
Top Coats (UV and non UV products)
Top coat is the final layer on MDF. Generally called ‘lacquer', It is already pigmented and applied for cosmetic (gloss, mat) and / or protective purpose (dust, pollution, ultraviolet). This layer is applied in a single layer.
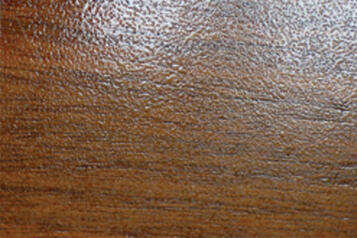
This issue appears when there is either too much air added to the spray pattern or too much product applied in one layer on the part.
To solve any orange peel effect, we recommend to use Airmix® technology :
- For manual application, use the XCITE™ LIGHT AIRMIX® MANUAL SPRAY GUN gun with our genuine Airmix® tip
- For automatic application, use the AVX AUTOMATIC AIRMIX® SPRAY GUN with our genuine Airmix® tip
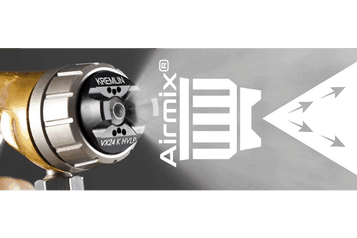
When you need an event layer on solid wood & a glossy finishing on MDF, Airmix® technology is particularly recommended to apply clear coat and top coat
Clear coat and top coat need to have certain thinness. In Airspray, you will need too many layers to achieve the film thickness you need and you will loose lots of paint with the overspray. In Airless® , you will apply too much paint.
Thanks to the low speed of the paint particle given we add 0.5 bar of air atomization, Airmix® keeps a maximum of solvent on the color particle during spraying. The 0.5 bar additional air accompanies the paint particle up to the subtract and prevent the air movement around the paint particle to avoid the “desolvation”. When you spray clear coat or top coat, the solvent will help the paint smoothing to have a glossy and even finishing. The non ”desolvation” with Airmix® technology helps avoiding problems like orange skin.