Hemming in Body in White
Hemming in Body in White
In car body construction, the bonding of the inner and outer panels of the doors, as well as, the front and tailgate represents a central process step. Dosing the right amount of adhesive ensures optimum sealing, reliable stability of the body, and the formation of a suitable substrate for the subsequent painting process.
In the hemming bonding process, the inner and outer panels of the doors are joined with adhesive. In addition, the inner panel edge is flanged or folded through the outer panel at an angle of 180° to give the structure mechanical stability.
Two techniques have become established in the market for applying the adhesive: bead and swirl application. The former is particularly suitable for standard applications and is predominant in automotive plants. The latter allows precise parameters to be set, but also requires additional know-how.
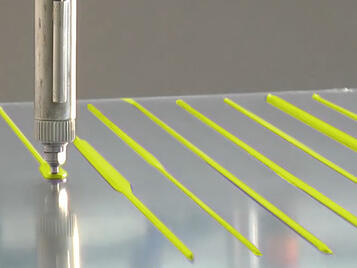
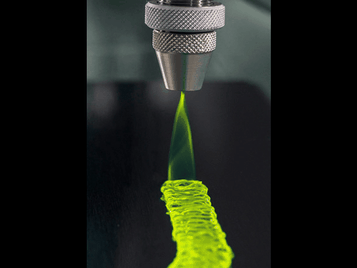
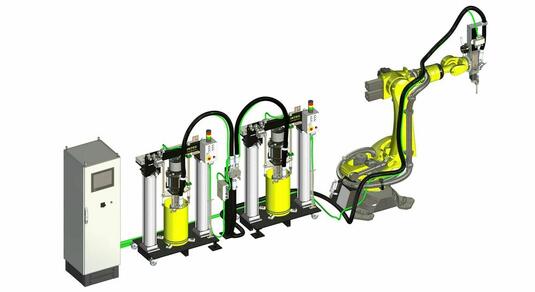
Our solution: A complete double barrel system
iNTEC Sames-KREMLIN offers you a complete conveying and application system for efficient hemming. In a standard double drum system, two powerful Ram stations pump highly viscous material from one container. The supplied control system ensures accurate conveying, as well as, optimal system tuning. The finished material feeds the dosing unit, which is mounted on a robot. Depending on the selected application method, the bead or swirl can now be applied to the sheet. Contact us for more information!
Important parameters for hemming
1 - Typology of the adhesive
Bead applications are predominant in the market because they can handle most adhesive types. Swirl applications, on the other hand, are not compatible with every adhesive as special fillers can cause the adhesive threads to break off. There is a risk of material being applied in the wrong place or of components, robots and grippers becoming contaminated by the uncontrolled tear-off thread of the adhesive. Similarly, deviations in material density per batch or per barrel lead to considerable problems in swirl application. Constant re-parameterization of the system would be the consequence, which would require additional costs and time. Likewise, the swirling of the material means that air and oil inclusions can occur after joining so that the overall quality of the application is reduced.
Conclusion: Most types of adhesive, even those without high quality requirements are easiest to apply by bead or bead-on-bead. The Swirl requires exact matching of the material to the production since density and temperature variations can directly affect the result and the quality of the bond.
2 - Component tolerance and distance to the workpiece
Depending on the technology, different distances to the workpiece are required. In the swirl process, distances of up to 50 mm are possible so that component deviations generally have no effect on the final result. In bead application, the distance to the sheet ideally corresponds to the cross-section of the bead (i.e. between 1.5 and 2.5 mm) in the case of bead bonding. Very large component tolerances can therefore quickly lead to a "nozzle crash" if the distance is too small during bonding.
Conclusion: Swirl applications offer the advantage of being able to compensate for component tolerances more easily due to the greater distance to the sheet. Bead applications are more susceptible here: large fluctuations in component geometries cause a "nozzle crash" more quickly.
3 - Knowledge and number of parameters
Different technologies require different levels of technical knowledge and corresponding staff training. Bead application is particularly simple, as only the flow, speed and temperature of the adhesive need to be set. Swirl application is more complex in comparison as the distance to the component and the rotation speed (E-Swirl) or the air proportion (P-Swirl) must also be controlled. If a parameter changes, the entire system must be adjusted.
Conclusion: Bead application requires a lower level of knowledge than swirl technology since fewer parameters have to be taken into account.
4 - Bead or flat surface application
In bead application, the distance between the nozzle and the component is fixed so that also the cross-section of the bead always remains constant. Due to the flexible distance, the adhesive width can be varied during swirl application. Care must only be taken to ensure that an even distribution of the adhesive requires an optimally set width.
Conclusion: In bead application, the geometry of the bead is determined by the size of the nozzle and the material flow. In swirl application, the application width of the adhesive can be varied specifically by the distance control.
5 - Assembly of the dosing unit
Both application methods require appropriate assembly of the dosing unit and the part. Bead application can be carried out either by robot or by stand; both variants are used in practice. P- and E-swirl application by robot is easier, since trajectory programming above the component lying on the table is less complex. The result is immediately visible to the programmer.
The same applies to any corrections: The amount and position of the adhesive are crucial to prevent the so-called "squeeze out" effect. When two sheets are flanged, excess adhesive escapes from the components and has to be removed manually afterwards. Automation of this process does not yet exist.
Conclusion: The type of application process (robot or stand) determines the complexity of programming and thus the effort of production. Precise trajectory control is essential to avoid possible errors and to set the correct quantity and position of the adhesive.
6 -Visual control
Efficient and reliable production is rounded off by a visual control system that monitors optimum adhesive application. Most plants already use 2D systems for this purpose. 3D monitoring systems are even more precise: They offer maximum process control but are more expensive to purchase.
Conclusion: Visual monitoring of adhesive application is always worthwhile, regardless of whether a 2D or 3D system is used. Due to their geometry, beads are easier to monitor than swirls.
Summary
Bead |
P-Swirl |
E-Swirl |
|
Complexity of the application | Simple technique, easy operation |
Complex operation due |
Complex operation due to numerous parameters |
Distance of the nozzle to the component |
2-3 mm, "nozzle crashs" are possible |
approx. 50 mm "nozzle crashs" are improbable |
approx. 50 mm "nozzle crashs" are improbable |
Programming effort | Medium | Simple | Simple |
Correction of the bead | Easy | Relatively complex | Relatively complex |
Compatibility with different types of adhesive | Suitable for all types of adhesives | Adhesive must be able to swirl | Adhesive must be able to swirl |
Flexibility | Normal | Normal | Very high, change between bead and swirl application possible |
Investment costs | Low | Rather low | High |
Visual Control | Simple | Difficult | Difficult |