Paint distribution group
Distribution group have to provide paint with the right conditions:
- viscosity & homogeneity
- pressure
- Flow
Depending on the production output, tank size will be adjusted to limit the manual filling and transfer operations (1 or 2 times/shift is a maximum).
To maximize the production line availability, distribution groups need to be designed with the most reliable components, and used not at the limit of their specifications. Upper version is always preferred, about pump size, pressure ratio, pipe diameters, etc...
Concept Layout
20L, 200L, 1000L can be used in the factories, coming directly from the supplier. This paint is concentrated and needs to be agitated + adjusted in viscosity while adding solvent.
A simple diaphragm pumps will transfer at the required flow paint from the drum to the preparation tank, and another one from the preparation tank to the distribution tank.
Usually made of stainless steel, the preparation tank will receive the concentrated paint and the solvent to be added. Solvent quantity can be controlled with a flowmeter. An air or electric agitator will mix the solvent and paint, but also stir it to make sure that all the solid contents are uniformly found in each area of the tank. The viscosity will be checked manually by an operator with the relevant cup (Ford 4mm, ISO 3mm, etc...).
The main functions of the preparation station are:
- Paint transfer
- Viscosity adjustment
- Paint agitation (uniformity and homogeneity of the material)
It is generally operated manually, but it can be also automated.
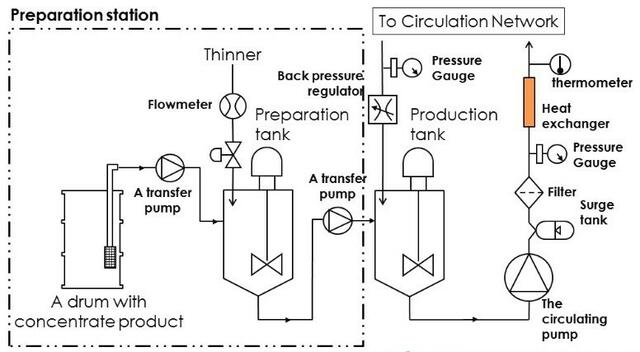
After the preparation tank, paint is transferred to the production tank, which will supply the different application stations in the production lines. It is continuously agitated, to keep the paint homogeneous. Sometimes, it can be temperature controlled, with a double skin tank receiving tempered water or with heat exchangers further in the supply pipes.
The main component in a PCS (Paint Circulating System) is the circulating pump. It has to provide the paint at the right pressure and the required flow for all the application stations. The dynamic pressure needs to be as stable as possible, to limit the interferences for the application devices usually sensitive to pressure peaks leading to variations in the application flow. The pump ratio needs to be sufficient to supply the required pressure.
The pump volume has to be adjusted according the required maximum flow, in order to limit the strokes per minutes for a longer life (MTBF increased).
To absorb the pump output pressure peaks, we can use surge tanks acting as a dynamic capacitor reducing the peaks. Some pump technologies do not need any surge tank due to their stable output pressure.
Pressure gauges are used to monitor the pressure at the output of the pump, and then on the return line.
We install filters after the pump medium pressure cartridge filter adapted to the working conditions (mesh size & pressure), and then on the return line low pressure bag filters, to make sure that the paint is coming back clean in the production tank.
The back-pressure regulator (BPR) will adjust the last point of pressure before the production tank (no pressure). It will fix all the pressure points in the upstream paint distribution lines, depending on pressure drops linked to the flow, viscosity and line geometry (diameters, angle and inner shapes). Low shear BPR will be preferred, especially for waterborne paint sensitive to mechanical stress.
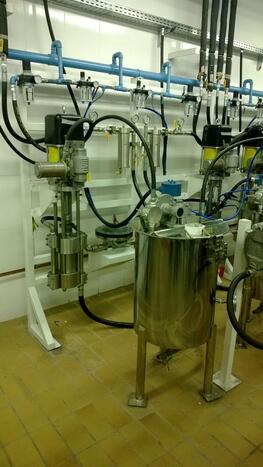
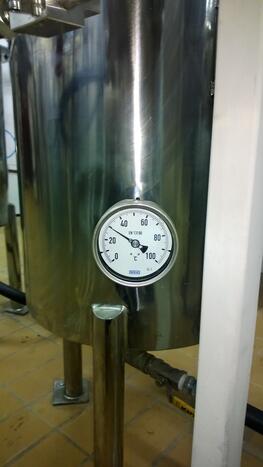
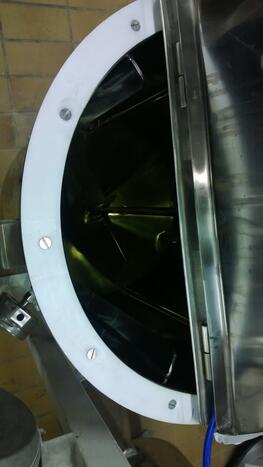
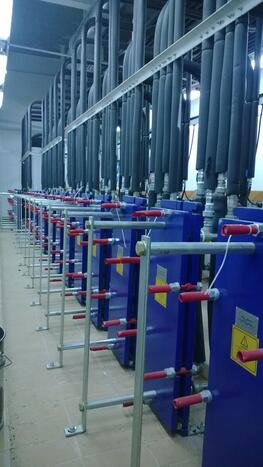
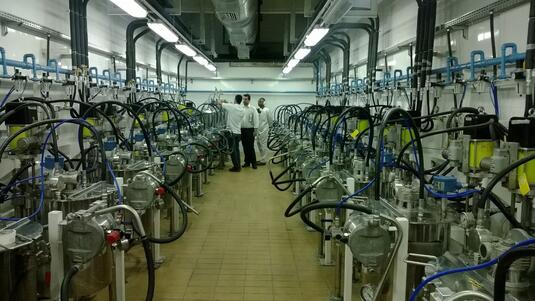
A paint mixroom or paint kitchen contains all the distribution groups, usually one per color.
Environment is tempered and kept clean. Depending of the material, the area is hazardous, and needs specific equipments to be installed inside for safety reasons.
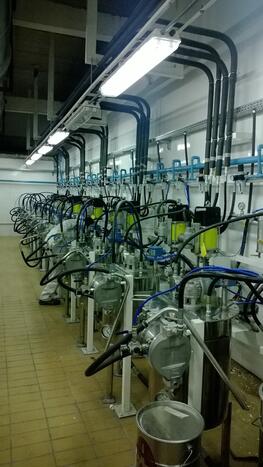
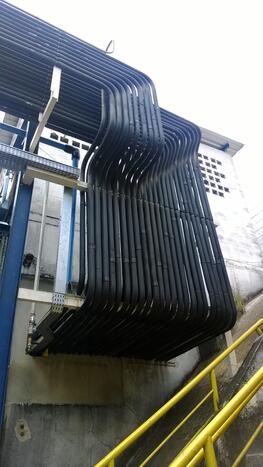
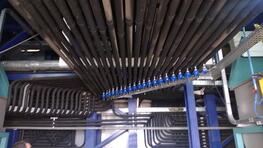
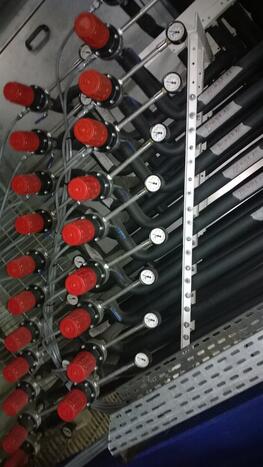