Rotating bell
The bell cup ensures uniformity of the droplet size spectrum leading to high finishing results.
Depending on its paint rheology, pattern size & the atomization level required, the proper bell cup must be chosen in the range of 35mm to 80mm diameter with concave or exponential shapes.
The 1st level of high speed bell cups are made of aluminum for a lightweight design & compatibility with most of paints. For an even longer bell cup life & for usage with specialty paints, Sames recommends titanium-made bell cups due to their high abrasion resistance. All bell cups have a distributor made in titanium.

Bell spraying technology
Rotary bell atomization is a high energy process which creates an optimal spectrum of droplet sizes for paint application. Flowing from a central injector, the paint is dispersed from the center to the edges of a bell cup rotating at a high speed (usually from 25 to 70krpm). Centrifugal forces create paint ligaments that are cut into droplets in the air. The paint cloud is then shaped and transported by the shaping airflow, and generally enhanced inside an electrostatic field, providing an extremely high transfer efficiency.
The higher the paint viscosity, the higher the bell cup rotation needs to be to get the same droplet spectrum. The high voltage effect helps to decrease the droplet sizes resulting in a uniform film with a wet condition & a preferred metallic flake orientation rearranged with Vortex shaping air on the part coated.
How does it work?
An air driven turbine moves a bell cup at a high rotation speed proportionate to the air flow & pressure. The speed reading is made simply by the noise frequency analysis invented by Sames Kremlin.
The sound sensor provides accurate speed measurement (<1%) and reliability, it is the best alternative to the conventional optic signal record which has a fragile plastic fiber and is sensitive to dirt & paint.
The bell cup, with its lightweight design, has been precisely balanced to reach this high rotating speed. Manufactured with the highest precision standards for the aeronautic & aerospace industries, the bell cup is constructed of aluminum or titanium.
As a result of designing our own Sames turbines, we have complete control over the performance of the atomizers.
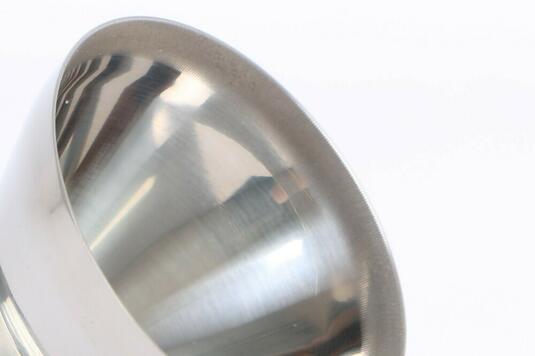
Serrated or not serrated bell cup ?
Bell cup serration
The serration gives the best finishing performances.
There are two mainstreams about serrations that Sames is not following : one is cross serrration and the other is no serration bell cups.
After years of paint trials in customer facilities, laboratories and computer assisted simulations, Sames is convinced that straight serration gives same atomization effect than cross serration, with a more robust process of manufacturing. The serration is helping a lot to calibrate the size of droplets, which gives the finishing results of the film build.
No serration is not recommended by Sames for most of paint process :
- Automotive carbody primer, base coat and clear coat have to use straight serration for high finishing results.
- General industry may use a wide variety of paint (viscosity, chemistry, resistivity, multi-component...) in a wide variety of process. We consider that a not serrated bell cup might be used with paint which dries very fast, and fill the serration, up to fill the bell cup itself. In this kind of specific case, not serrated bell cups allow easier cleaning and sometimes bubbles can be avoid.
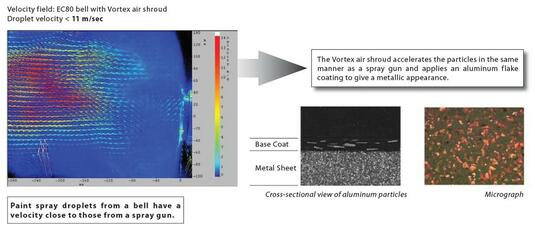
Metallic applications
In base coat and top coat, the metallic effect of the paint can be challenged with the electrostatic effect and the low particle speed bell technology. In the field, metallic flakes are getting oriented and lose their reflecting effect inside the film build with regular orientations. We have designed specific bell head systems with efficient air shroud effect and high rotating speed with wide bell cup diameter.
This principle gets very close to the gun application quality in term of color appearance but still get the benefits of the bell process with higher transfer efficiency and uniform surface.
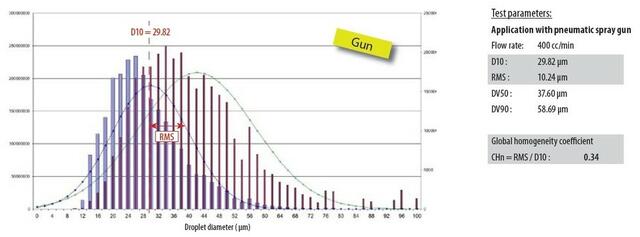
Equivalent droplet dispersion with Bell
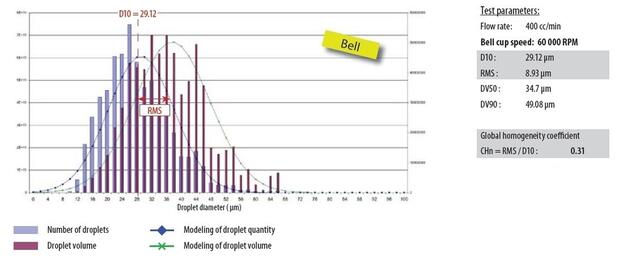
HIGH Flow Bell applications
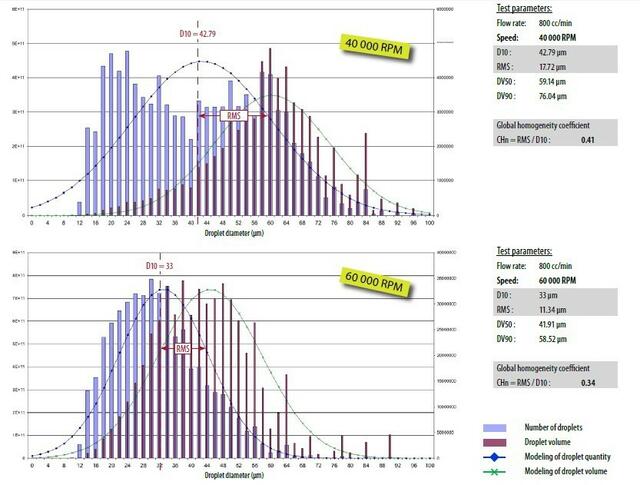